BLIND FLANGES
A blind flange is a round plate which has all the corresponding bolt holes but no center hole, and because of this characteristic, this flange is used to close the ends of the piping systems and the openings of the pressure vessels. It also allows easy access to the interior of a line or vessel once it has been sealed and must be reopened. Blind Flanges are commonly used in petrochemicals, pipe engineering, utilities and water works.
For best fitting of blind flanges we check for following :
- Outer Diameter of body
- Outer Diameter of body
- Straightness and alignment of the bolt hole
- Thickness of the Blind
A Blind Flange has no bore, and is used to close ends of piping systems. A blind flange also permits easy access to a line ones it has been sealed.
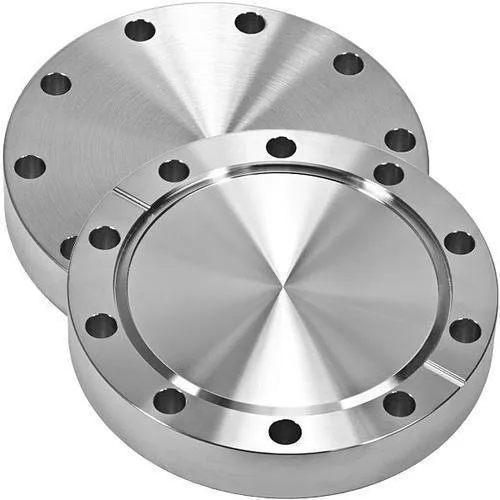
SLIP ON FLANGES
Sliding pipe clamps. These pipe flanges slide on the pipe. They are made with an inside diameter slightly larger than the outside diameter of the pipe. These fasteners are connected to the pipe via a corner weld at the top and bottom of the flange. The weld neck flanges have a longer life than the slip-on flanges.
The sliding flanges are all slightly larger than the O. D. of the pipe. They are preferred to weld neck flanges by many users because of their lower initial cost, but the final cost of installation is probably not much less than that of the weld neck flange due to the weld additional involved.
Advantages of using Highborn Slip-On flanges are as follows:
- Low cost installation
- Less time needed to spent on ensuring the accuracy of the cut pipe
- They are somewhat easier to align
- The slip-on flanges have low hub because the pipe slips into the flange before welding
- The flange is welded both inside and outside to provide sufficient strength
- They prevent leakage
They are preferred to weld neck flanges by many users because of their lower initial cost, but the final cost of installation is probably not much less than that of the weld neck flange due to the weld additional involved.
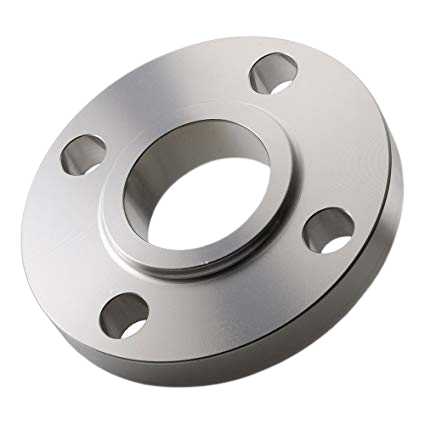
THREADED FLANGES
Threaded pipe flanges are similar to threaded pipe flanges except that the threaded pipe flange bore has tapered threads. Threaded pipe flanges are used with pipes that have external threads. This type of connection is fast and simple but not suitable for high pressure and temperature applications. Threaded flanges are mainly used in utilities such as air and water. Its main merit is that it can be assembled without welding, explaining its use in low pressure services at ordinary atmospheric temperatures, and in highly explosive areas where welding creates a hazard.
The benefit of these pipe flanges is that it can be attached without welding.
The ASME B16.5 and ASME 16.47 pipe flanges and flange fittings standard covers pressure-temperature ratings, materials, dimensions, tolerances, marking, testing, and methods of designating openings for pipe flanges and flanged fittings.
Threaded Flanges can be used in extremely high pressure services, thus proving impeccable working capacities. Our threaded flanges, threaded pipe flanges and stainless steel threaded flanges can be customized as per the client’s requirement.
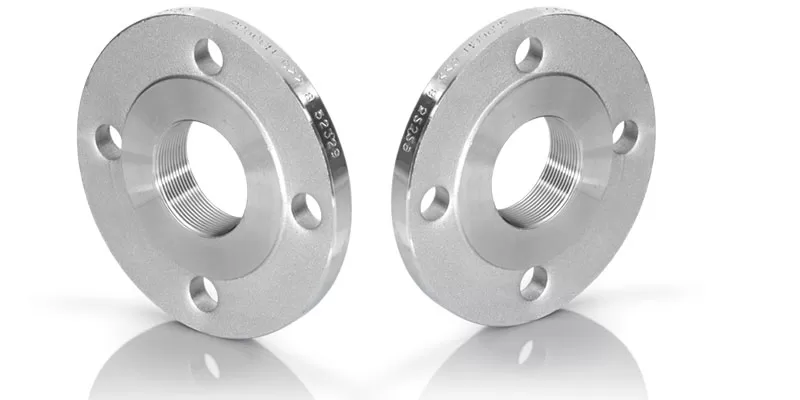
ORIFICE FLANGES
Orifice flanges usually apply to measure the volumetric flow of liquids and gases through a pipe. Two orifice flanges are referred to as an orifice flange union. Each flange is equipped with two valves to measure the pressure drop of the flow through an orifice plate. The orifice plates do not come with the flanges and are dimensioned according to the requirements of the process. Two screws are used to spread the flanges to change the orifice plate. This flange is normally available in welded, sliding and threaded flanges. The orifice flanges generally have an elevated face. They are usually used for a general and mechanical engineering purpose and also for structural purpose.
Orifice Flanges generally come with either Raised Faces or RTJ (Ring Type Joint) facings. They are, for all intensive purposes, the same as weld neck and slip on flanges with extra machining.
We also make a set Orifice Flanges, where a Orifice Plate is mounted and a jack screw is machined. This jack screw is used to facilitate separating the flanges for inspection or replacement of the Orifice Plate and gaskets.
The range of orifice flanges covers all standard sizes and ranges, and all common flange materials. Flanges are available in Welding Neck, Slip On, and Threaded form, and are typically supplied with two 1/2″ NPT tappings in each flange.
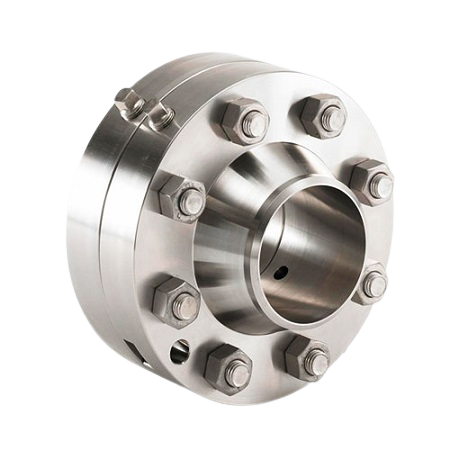
LARGE DIAMETER FLANGES
A Large Diameter flange is a metal ring that is used to connect valves, pipes, pumps and other equipment that is necessary to form pipelines. The Large Diameter flange also allows people to have easy inspection, rapid modification, and easy and quick access to clean the pipes.
The ASME/ANSI B16.47 Large Diameter Steel Flanges include NPS 26 through NPS 60. This standard covers pressure ratings, temperature ratings, materials, dimensions, tolerances, marking and testing for flanges of this size with rating class designations 150, 300, 600, 900, 1500 and 2500.
The ASME/ANSI B16.47 Large Diameter Steel Flanges include NPS 26 through NPS 60. This standard covers pressure ratings, temperature ratings, materials, dimensions, tolerances, marking and testing for flanges of this size with rating class designations 150, 300, 600, 900, 1500 and 2500.
The flanges are made in multiple ways. Some have lips, while others do not. Nearly every type of flange has a seal attached to it in order to preclude any type of leaks from the pipeline.
Highborn creates a significant volume of large diameter flanges for the biggest jobs in the energy and industrial fields. We can create a variety of large diameter sizes and configurations, using numerous suitable materials of construction for every application.
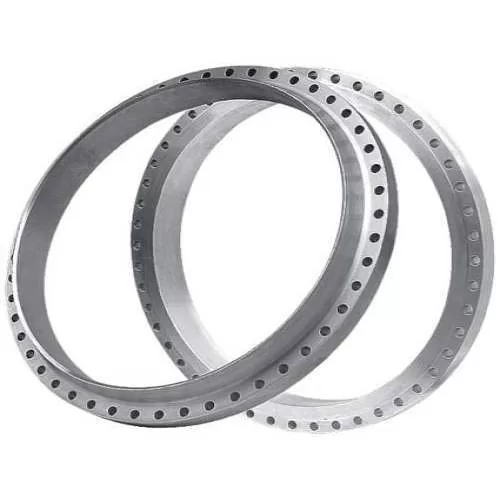
SAE FLANGES
Ranges of SAE flanges and hydraulic flanges are manufactured in Highborn Flanges and Fittings that meet the relevant international standards. These flanges find application in industries where flanged joints are encountered during manufacturing and maintenance tasks. Our wide range of SAE flanges can also be customized according to the drawings and specifications provided by customers. These flanges are used on oil hydraulic systems in many fields (shipbuilding, mobile hydraulic equipment, machine tools, earth moving machines, etc… ) and where there is passage of oil under pressure.
SAE Flanges are designed as per SAE J 518 C standards worldwide & VE-LOCK SAE Flanges can be Interchangeable.
The design for the SAE System calls for Forged Flanges with Sleeves made from weldable material. In order to reduce costs, we have introduced a two piece system where the sleeve & the Flange were combined into one Piece. Such a system is easily adaptable to both Butt Weld and Socket weld Systems. However in practice, the two piece system is used mainly for Socket Weld Flanges for cost considerations.
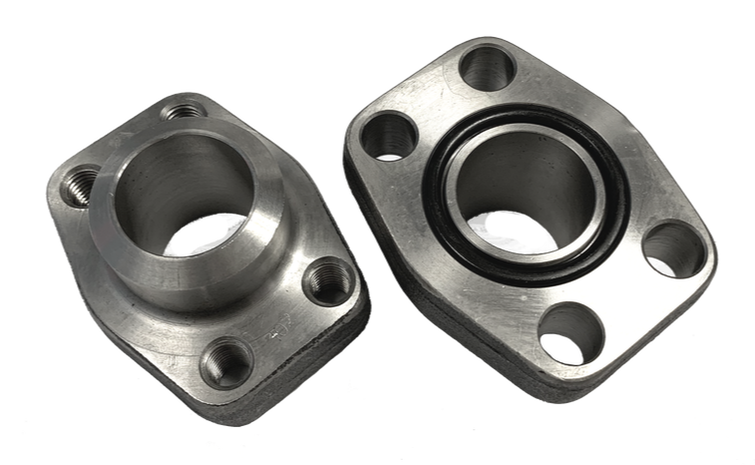
LAP JOINT FLANGES
The lap joint flange has two components, one stub end, and loose backing flange. The end piece is welded end to end to the pipe and the support flange moves freely on the pipe. The support flange may be of different material from the stub material and normally of carbon steel to save cost. The cover flange is used when frequent disassembling is required, and space is limited. The flange of the lap joint is almost identical to a slip-on flange, except that it has a radius at the intersection of the bore and flange face.
These flanges are nearly identical to a Slip On flange with the exception of a radius at the intersection of the flange face and the bore to accommodate the flanged portion of the Stub End.
The lap joint flange is practically identical to a slip-on flange except it has a radius at the intersection of the bore and flange face. This radius is necessary to have the flange accommodate a lap joint stub end. Normally, a lap joint flange and a lap joint stub end are mated together is an assembly system. Sizes we make range from 1/2″ to 64″ (and much larger size according to customers’ demands).
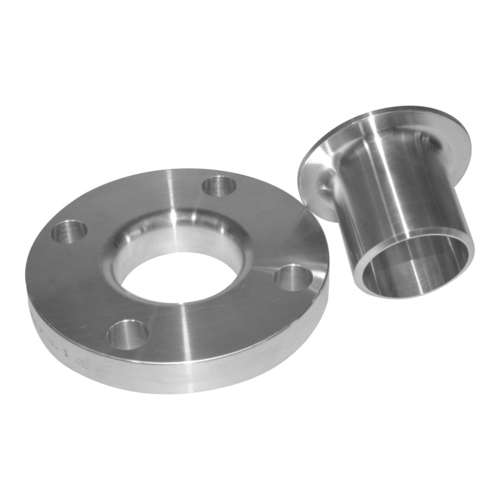
WELD-NECK FLANGES
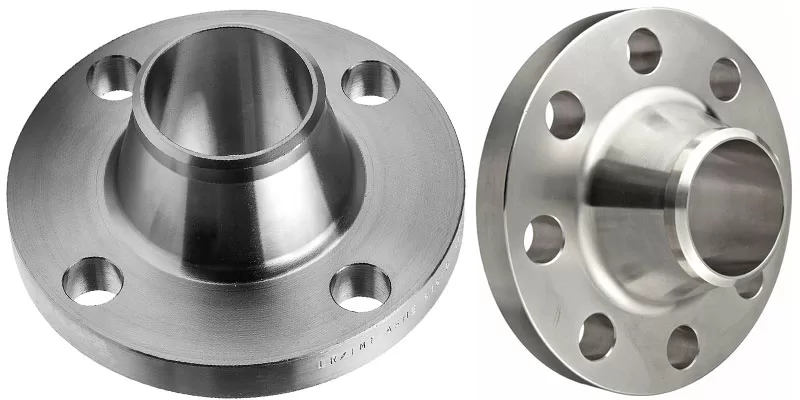
LONG WELD-NECK FLANGE
Long-necked flanges, also known as LWN flanges, are specialized components utilized primarily in high-pressure and high-temperature scenarios, notably in the oil and gas industry. Unlike standard weld neck flanges, LWN flanges feature an elongated neck that guides the pipe into the flange, providing critical reinforcement. This reinforcement is essential for safety in demanding industrial applications. LWN flanges find their main application in vessels where an extended neck is necessary, offering a unique design for specific connectivity requirements. These flanges are commonly used in the chemical and petroleum industries and are preferred in situations involving high stress and temperature fluctuations, as indicated by ASME 16.47 and ASME 16.5 standards.
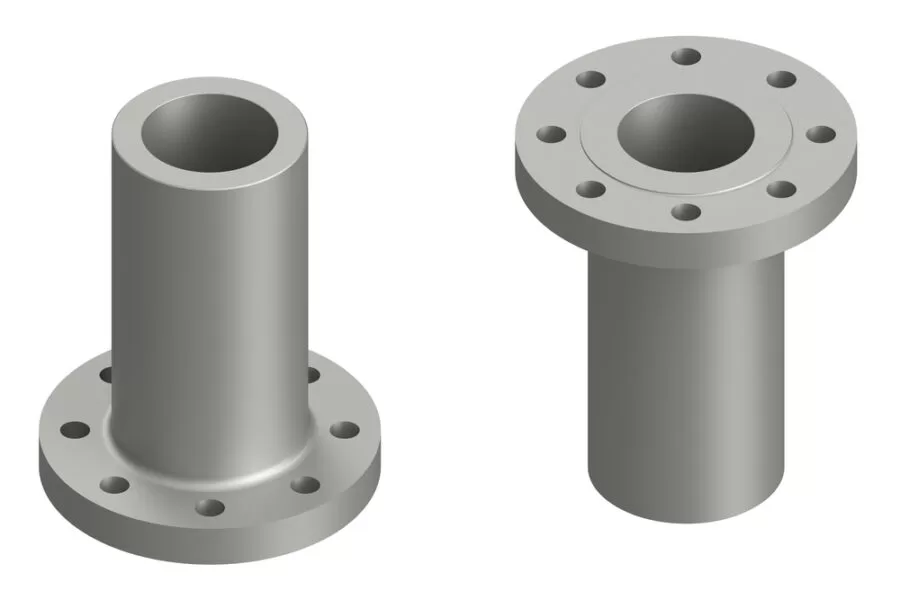